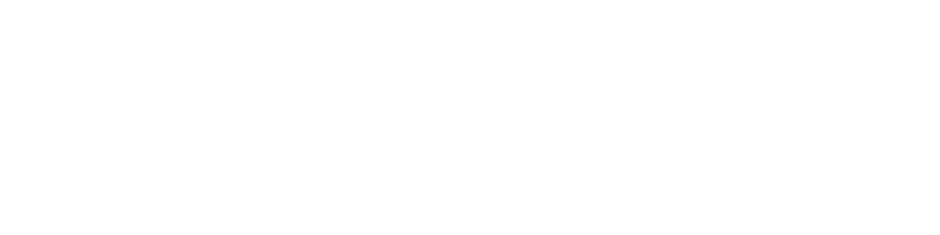
WE SUPPORT THE ENTIRE RETAIL GROWTH STRATEGY
We translate leading retailers’ marketing strategies into store-level successes through our network of best-in-class print/fabrication and fulfillment facilities, a full-service in-house design agency and AccuStore, our proprietary technology platform for streamlining in-store marketing programs.
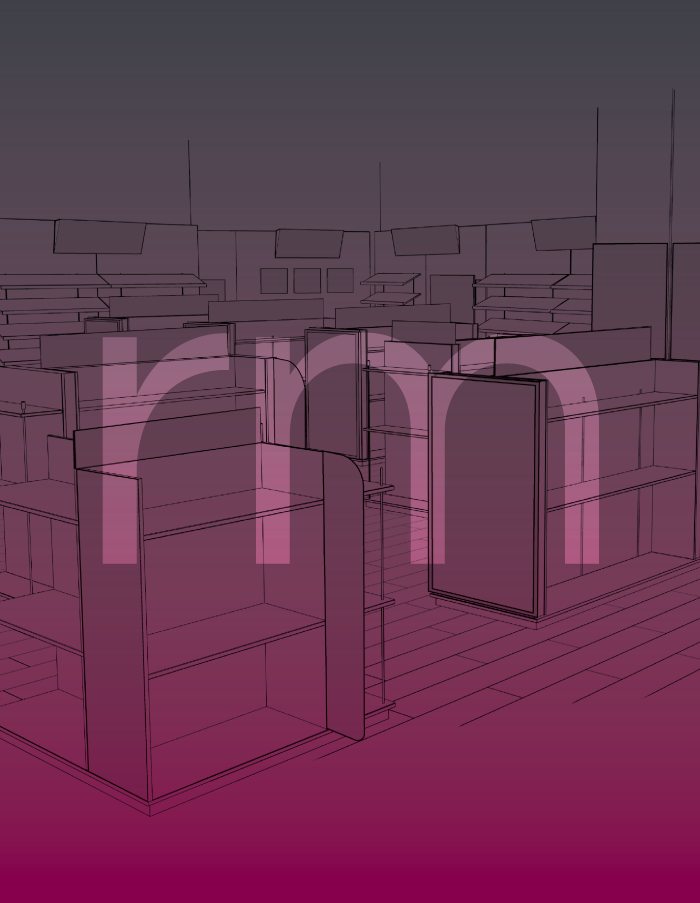
AWARD-WINNING
Industry-leading expertise to support retail design and growth strategies.
G7-CERTIFIED
Master quality and color consistency.
ACCUSTORE
Optimize production, distribution, and execution.
OPTIMIZED
Reduce transit times, transport costs, and emissions.
STRATEGY & DESIGN
GSP offers an in-house creative agency renowned for thought leadership in marketing, design and branding. Our team consists of graphic designers, art directors, creative directors, photographers, industrial designers and fabricators. GSP helps retailers connect with their shoppers and lift sales.
- Brand and identity creation
- Multi-channel campaign development
- Visual merchandising
- Private label packaging
- Digital signage content
- Food, product and fashion photography
PRINT & PRODUCTION
GSP provides advanced printing, fabrication, and fulfillment services for convenience, grocery, fashion, and specialty retail. Our customers benefit from the latest capabilities in grand format production, fabric graphics and sustainable printing. The AccuStore platform automates advanced workflows such as variable data printing/web-to-print programs and multi-plant fulfillment.
- G7-certified master quality & color
- Optimized shipping
- Automated distributions
- SGP-certified print & fulfillment center
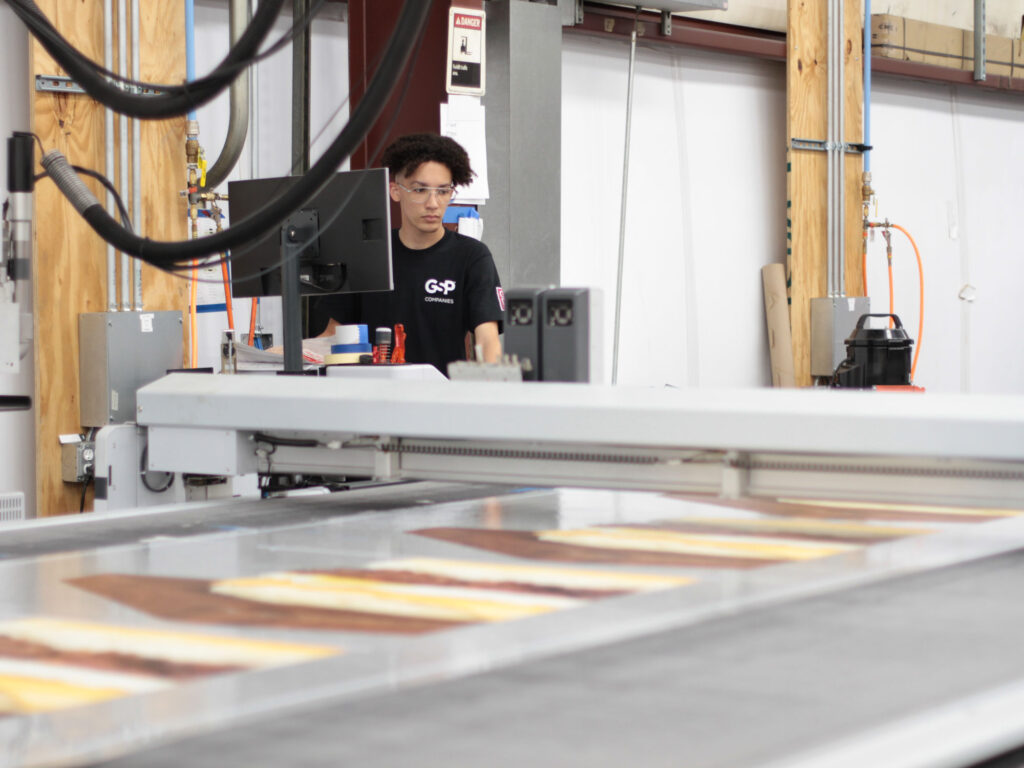
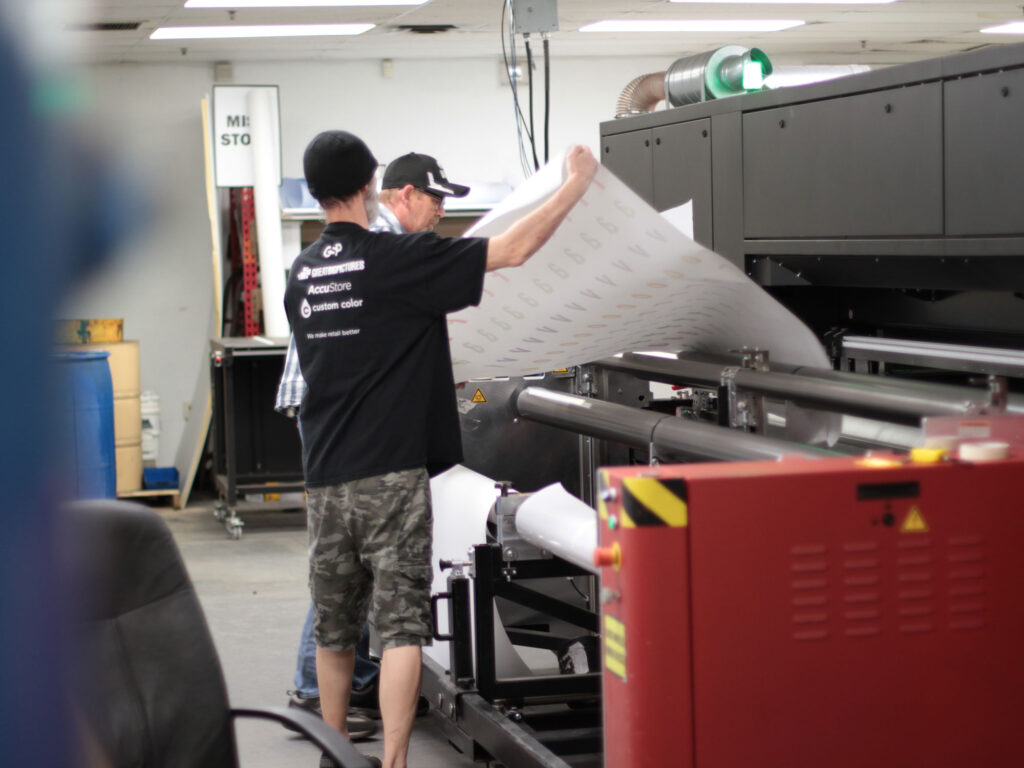
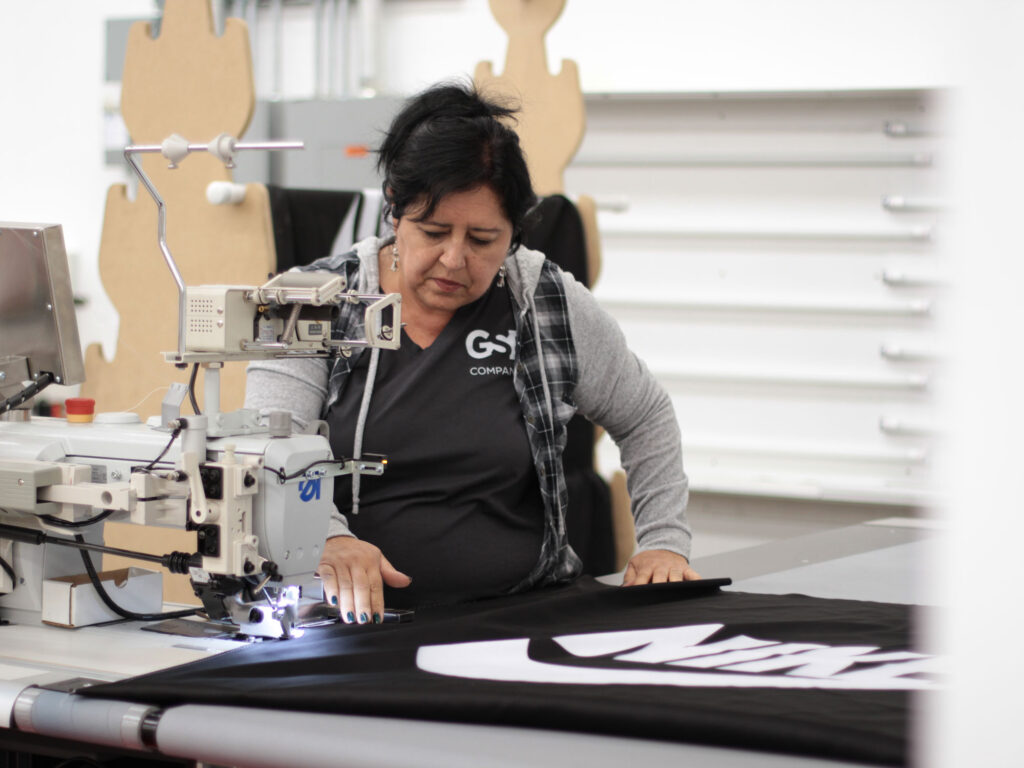
STORE-SPECIFIC FULFILLMENT
GSP leverages our industry-leading profiling platform, AccuStore, to the specific needs of each store. Our automated system enables us to fulfill complicated POP orders at a best-in-class rate of accuracy, and a store specific kit and marketing guide is sent to each site. This reduces waste, freight costs, and environmental impact.
- 100% store-specific POP kits
- Industry leading speed & accuracy
- Streamlined store support
- Dedicated account management
- Store-specific, visual placement guides
OPTIMIZED DISTRIBUTION
GSP Clients place one large order for multiple stores. AccuStore automatically allocates the printing and fulfillment to the plant that is closest to each store, creating multiples of savings using GSP’s optimized carrier system, in shorter freight hauls.
- Reduces transit times & costs
- Increases speed to market
- Reduces transport emissions
ACCUSTORE
AccuStore powers full retail marketing processes—from building and maintaining store profiles to writing distributions for in-store campaigns. AccuStore’s digital asset module tracks content and approvals of multiple stake holders. The mobile app provides survey functions that operate in any location on any type of device.
- Store Profiling
- Digital Asset Management
- Campaign Management
- Store Portal
- Store-specific marketing guides
- Execution management